3D iMplants
Home-3D iMplants
About Us
The primary objective is to develop personalized 3D implants. It currently works on developing different types of orthopedic implants such as screws for bone regeneration as well as personalized dental implants. It develops 3D printed objects for educational purposes for students to understand the anatomical features of the body in a better way possible.
- Founders: Dr.Swaminathan, Dr. Anuradha
- Fund raised by NIDHI PRAYAS
- anuradha@bioengg.sastra.edu
- Startup Domain: 3D Printing,Healthcare
Our Work
3D implants provide 3D printed on-demand solutions in the field of healthcare, prosthetics and surgical aids. 3D printed biodegradable porous screws with tunable dimensions for bone injuries were developed for better tissue-integration and biocompatibility compared to commercially available non-degradable metallic screws. 3D implants have developed personalized breathable, washable lightweight orthopedic hand casts for fractured arm replacing the conventional plaster cast. This is one of the promising projects where perfect-fit, well-ventilated, easily worn and shower-friendly hand casts customized for patients. 3D implants also offer anatomical models for critical surgery planning that contributes to faster, less traumatic and more precise surgery. Also, 3D Implants developed ventilator splits and flow limiters using 3D printing process to meet the increasing ventilator demand during the emergency COVID19 situations. Face masks and face shields have also 3D printed during the covid emergency.
Fig. [A] Biodegradable porous orthopaedic screws;
[B] Personalized breathable, washable lightweight orthopedic hand casts.
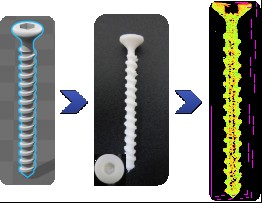
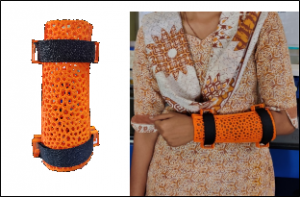
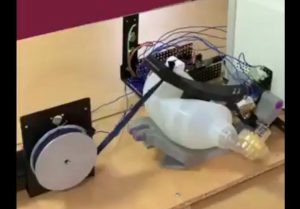
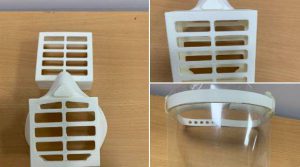
Ventilator Splitters
PLA based 3D printed 2-way and 4-way splitters for ventilators were designed, developed and tested successfully in TN RGGH(MMC) to address the ventilator shortage in COVID-19 pandemic. 3D splits which are connected to ventilator ports can ventilate four patients at a time. Face masks, gears & shields were 3D printed for personnel in Covid 19 relief work. They also developed AMBU bag based ventilator which can work on both volume and pressure modes.
How to make the life of armless better ?
The main objective is to model a 3D printed bionic arm with motor and electronic circuits such that the arm could move in 7 different directions by brain signals. A 3D model is generated, enveloped and assembled using Solid works. All the motion and collision detection is analysed and then printed using Ultimaker bot. These parts are now filed and grinded wherever necessary and assembled. The respective tolerance for strings and motors are analysed and designed before printing. These stings are now connected with motors which when rotates, the corresponding finger would bend. Five motors are connected for five fingers. These S series servomotors are supplied from a 15V source. The input can be controlled by an arduino circuit. These inputs are gathered from EMG sensor which is connected with brain. With help of doctors, the EMG electrodes are inserted inside the respective muscle area, that will further sense the muscle movement. The signals from sensors is sent to another arduino board that converts muscle signals to proper amplified electrical signals and sends them to another arduino board circuit that is connected to motors which then facilitates the motion of fingers, wrist and elbow. This bionic arm will be fixed to an amputee.
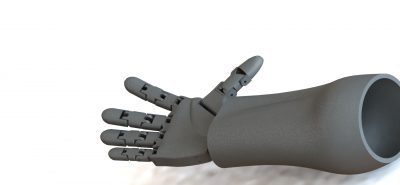
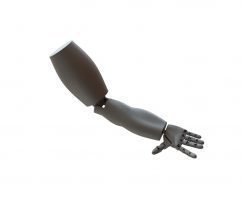